Why treat the fuel? Marine engines are designed to run on refinery grade fuel. However, the reality is that bunkered fuel has already logged many idle hours during storage and transportation. Stored fuel interacts with air and bacteria which introduce oxidation and biological contamination. This forms various polycyclic aromatic hydrocarbons (PAHs) as well as increases fuel viscosity. These newly formed molecular compounds (PAHs) are very stable leading to poor combustion reaction. In the end, low quality fuel contains reduced useful energy density causing incomplete combustion reaction. A fuel that does not burn completely ends up as soot in the air or on the transom.
What is the Green Fuel Catalyst technology? Catalyst or your ‘Onboard Mini Refinery’ consists of a patented Fitch® catalyst technology that is made of Heterogeneous Metallic Alloy Composition (HMAC). Catalyst alloy, consisting of a multiple different metals cracks the aromatic (non-reactive) hydrocarbon molecules, forming oxygen-containing compounds that have greater energy yield and better combustibility. More complete combustion means big savings in fuel expenses (reduced operating costs), less impact on the environment (reduced emissions), less intensive engine maintenance, less transom soot, and more range per tank.
Robust design – catalyst material (HMAC) is safely housed within steel core assembly where it is additionally secured with a rugged metal wire mesh. Steel core with catalyst material is housed by a canister which is made from SA 414 G (ASME) grade steel, and is rated up to 300 PSI (20 bar) of MAWP, and has been hydrotested at 390 PSI (26.5 bar). Catalyst lifetime is 10,000 operating hours after which the core assembly is recommended to be replaced.
Where is Green Fuel Catalyst to be installed? Installation on a marine vessel that is running on HFO, MGO or any other suitable hydrocarbon fuel type except the LNG is simple. Just locate a suitable place within the booster system after the mixing and heating units on its way to the Main Engine (ME) or the Auxiliary Engine (AE). It is very important to ensure that a multi pass effect is observed every time. This is to ensure that the fuel recirculated back from the ME or AE to the booster unit passes again through the fuel catalyst before being discharged back into the engine.
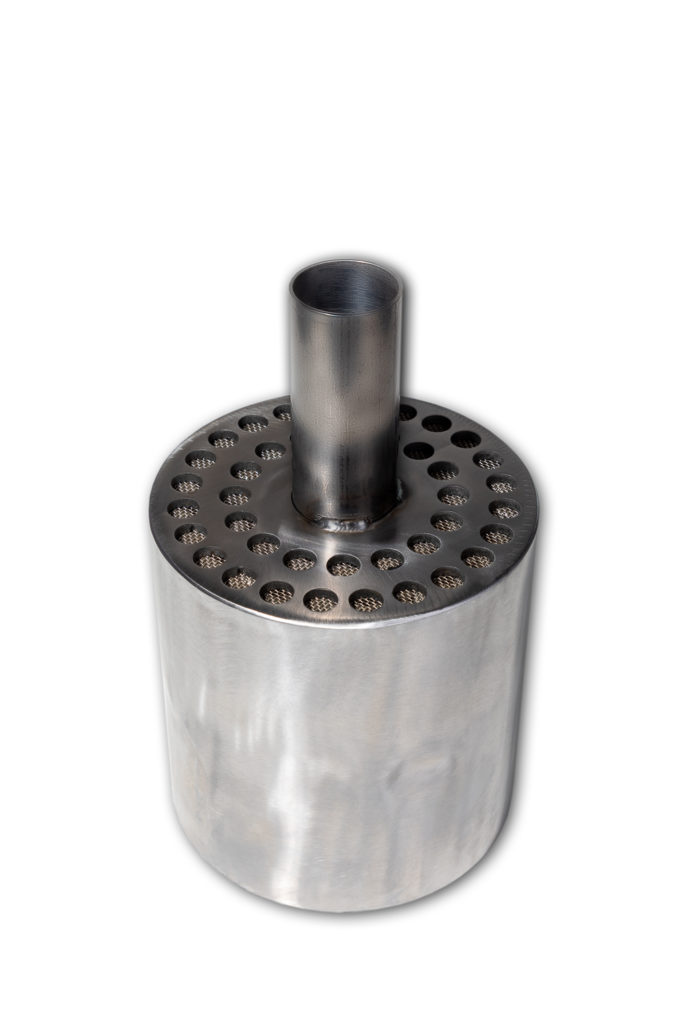
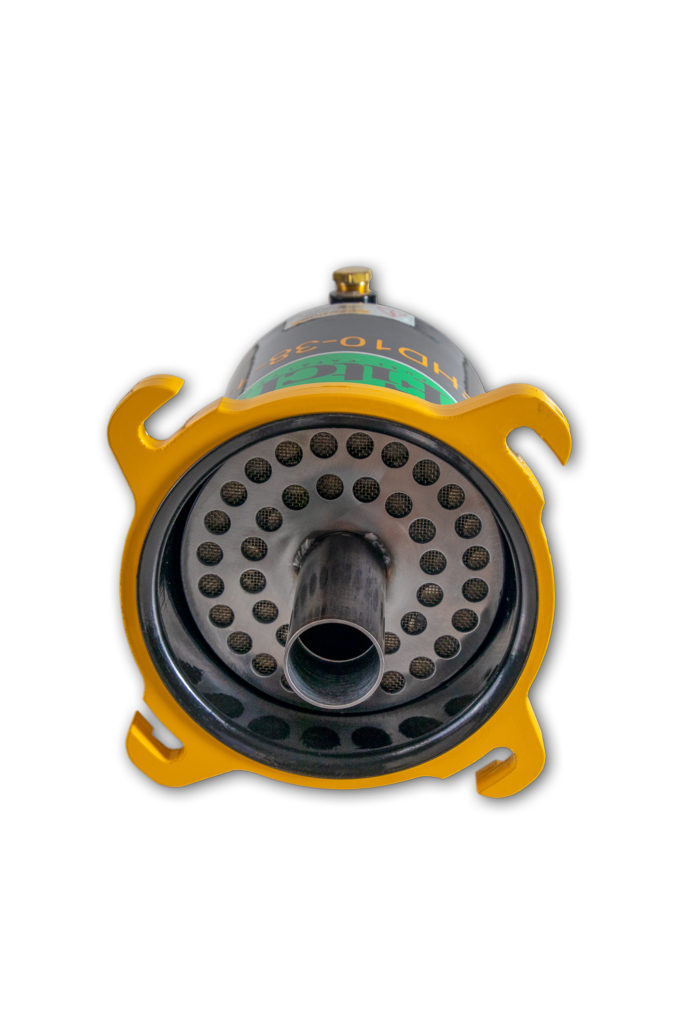
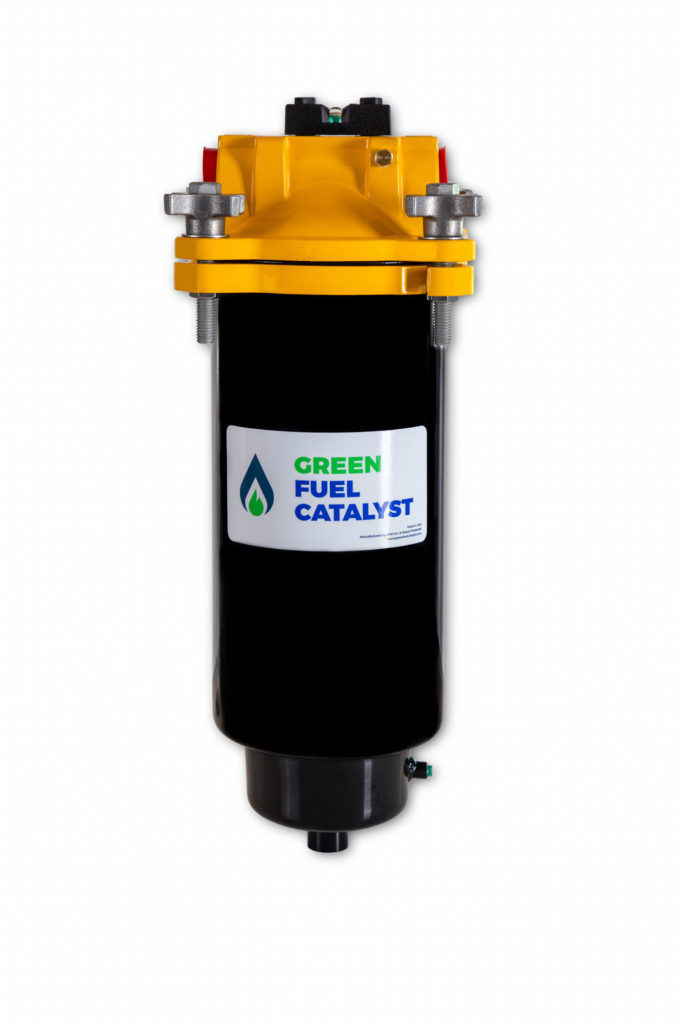
Applications
- Container ships
- Bulk carriers
- Oil & Chemical tankers
- Gas carriers
- Passenger ships
- Offshore service vessels
- Navy ships
- Cargo ships
- Fishing vessels
- Tug boats
- Inland navigation vessels
- Dredgers
- Yahts
- Roll-on, roll-off ships
Benefits
- Reduce fuel consumption by over 2%
- Reduces carbon footprint, pollution, emissions, greenhouse gases (CO, CO2, H-C, PM10, NOx, SOx)
- Fast payback with average ROI of 4-6 months
- Catalyst lifetime is 10,000 operating hours
- Induces more efficient fuel combustion
- Reduces soot and carbon buildup
- Improves fuel lubricity
- Improves horsepower & torque
- Improves cetane and reduces CCAI index
- Extends engine lifetime
- Minimizes injector, exhaust and fuel system maintenance
- No moving parts, no additives, no magnets
- Easy and simple installation
- Requires no extra maintenance for lighter fuels
- No significant pressure loss
- ABS, US Coast Guard, Lloyd’s, Det Norske Veritas, accepted