Green Fuel Catalyst is based on a patented Fitch® technology that’s manufactured in USA. It is used in Diesel, Gasoline, Natural Gas or Propane fired engines, turbines or burners improving fuel quality and combustibility while yielding more useful energy with reduced emissions and lowered operating costs. Within the power industry, applications can range from more than 50,000 horsepower (37,000 kW), down to small size boiler houses and local power generators where the power grid is not available.
Catalyst treated fuel burns more efficiently while reducing carbon build-up. This also reduces the frequency of heating system cleanings as well as the emissions of the greenhouse gases.
What is the Green Fuel Catalyst technology? Catalyst consists of a patented Fitch® catalyst technology that is made of Heterogeneous Metallic Alloy Composition (HMAC). Catalyst alloy, consisting of multiple different metals cracks the aromatic (non-reactive) hydrocarbon molecules, forming oxygen-containing compounds that have greater energy yield and better combustibility.
In natural gas applications catalyst promotes Oxygenation resulting in a more effective combustion reaction which gives higher energy yield, and less harmful emissions (CO, NOx) along with reduced carbon footprint (CO2).
Restored fuel quality and the enhanced combustion reaction result in over 2% fuel savings while providing improved fuel lubricity (liquid hydrocarbon applications), reduced carbon footprint and lowered emissions. Catalyst has an average ROI of 4-6 service months if utilized 24 hours per day.
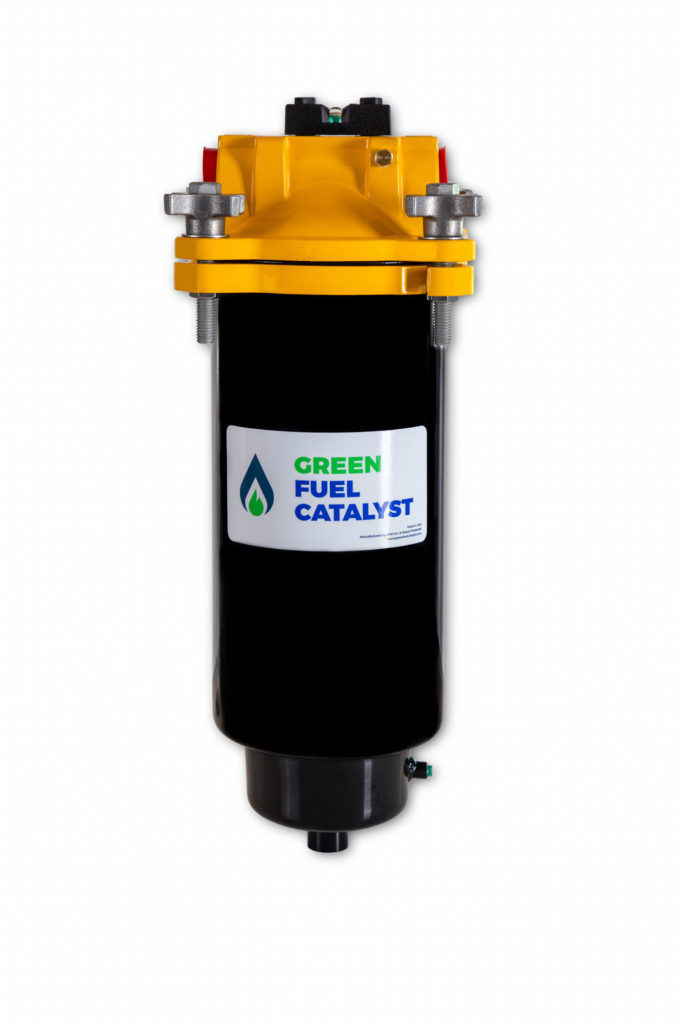
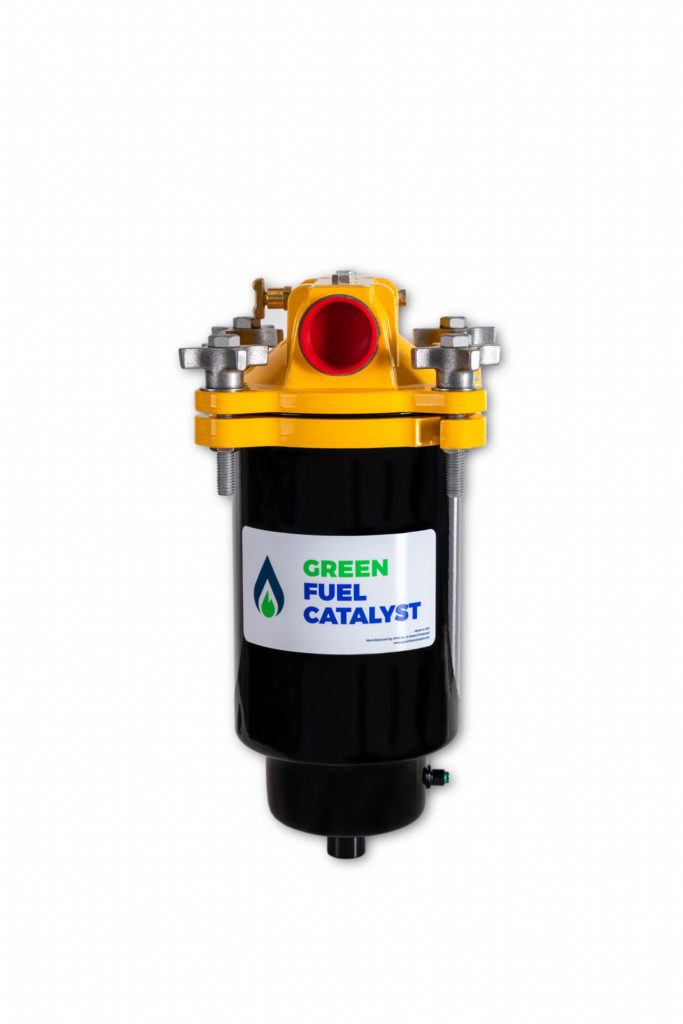
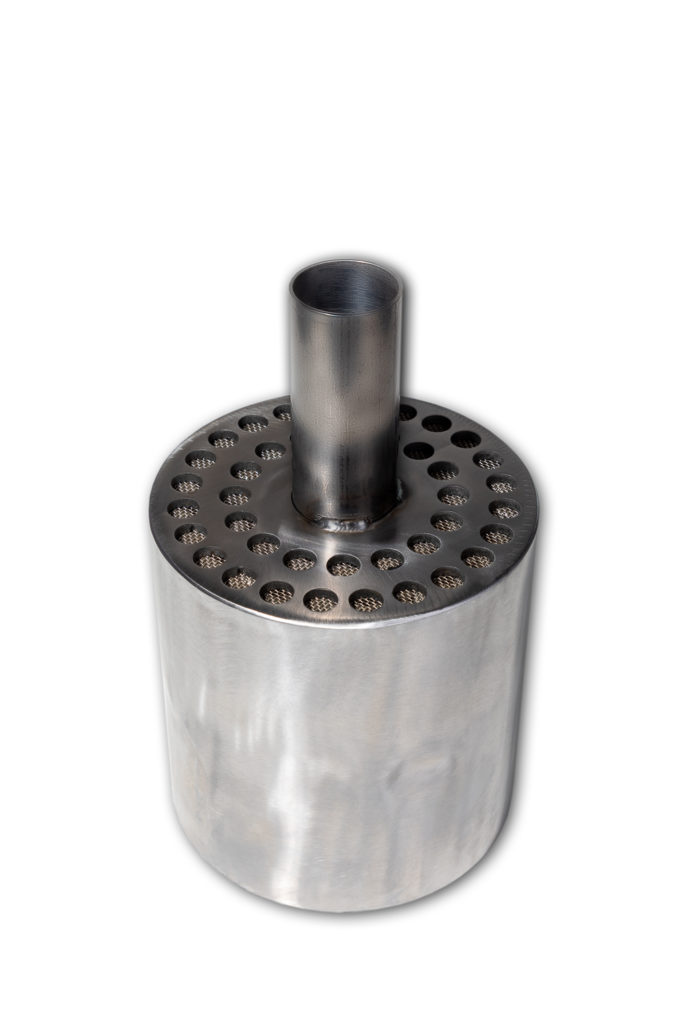
Where is Green fuel catalyst to be installed in natural gas applications? Installation in the natural gas applications for turbines, gas generators, burners is simple. Typically a bypass installation is used for the ease of catalyst maintenance, servicing and future replacement needs. Catalyst should be installed within 10m or so from the generator/turbine/burner however, installation distance should not exceed 20-25 meters in any case.
Where is Green Fuel Catalyst to be installed on a stationary engine in applications for the liquid fuels? Installation on a stationary engine that is running on HFO, MGO or any other suitable hydrocarbon fuel type except the LNG is simple. Just locate a suitable place within the booster system after the mixing and heating units on its way to the engine. It is very important that a multi pass effect is observed every time in the fuel oil applications. This is to ensure that the fuel recirculated back from the engine to the booster unit passes again through the fuel catalyst before being discharged back into the engine. Operating pressure in the line where catalyst is installed should not exceed 20 bar.
Applications
- Large industrial plants for power and heat generation
- Boiler houses for steam or heat generation
- Applicable for liquid oil or natural gas fired engines or burners
Benefits
- Reduce fuel consumption by over 2%
- Average ROI is 4-6 operating months at 24 hour load cycle per day
- Reduce visible smoke
- Improve “light-off ” time
- Reduce annual maintenance
- Reduce emissions of NOx, CO, CO2, H-C
- Increase H/C ratio
- Polynuclear aromatics reduced
- Aliphatic compounds increased
- Improve combustion
- Minimize injector, exhaust and fuel system maintenance
- No moving parts, no additives, no magnets
- Easy and simple installation after the fuel filter
- Reduce bacterial growth
- Does not void the engine manufacturer warranty, UL certified
- Catalyst lifetime for liquid fuels in power generation or heating applications is 10,000 operating hours
- Catalyst lifetime for natural gas is 20,000 operating hours